はじめに
電気自動車の性能向上に伴い、バッテリーの高出力化が進み、それに伴う電力消費の増加により発熱量も増大しています。このため、バッテリーの安定した動作を確保し、性能を最大限に引き出すためには、効率的な冷却構造の設計が不可欠となります。特に、バッテリーパックの温度管理は、セルの寿命や安全性に直結するため、最適な放熱機構の設計が求められます。
本事例では、フィン付きヒートシンク構造を対象とし、熱交換効率の向上を目的とした最適化を実施しました。まず、ヒートシンクのフィン形状や配置をパラメトリック化し、多様な設計パターンを柔軟に評価できるモデルを構築しました。このフルパラメトリック化されたヒートシンクモデルとCFD解析ツールを連携させることで、冷却性能を最大化するための自動最適化プロセスを確立し、より効果的な放熱設計を実現することを目指します。このような最適化は、バッテリーの熱管理能力を向上させ、電気自動車の信頼性向上や長寿命化に貢献できることが期待されます。
■使用ソフトウェア:CAESES、CFD解析ツール
最適化概要
最適化計算のためのフルパラメトリックモデルはCAESESによって作成されました。ヒートシンクのフィン長さや幅、配置角が設計変数となるよう構築されており、各パラメータの値によって形状が柔軟に変形するように定義されています。
図1~3:設定された設計変数による形状変形
CAESESで接続されたCFD解析ツールによって、シミュレーションによる定量的な評価が行われます。設定された以下の解析条件により、各形状(設計候補)の解析が行われます。
1.物理モデル:定常、流体構造連成(固体領域:銅、流体領域:空気)、Standard K-epsilon乱流モデル
2.メッシュモデル:非構造格子、約50,000セル
3.境界条件:
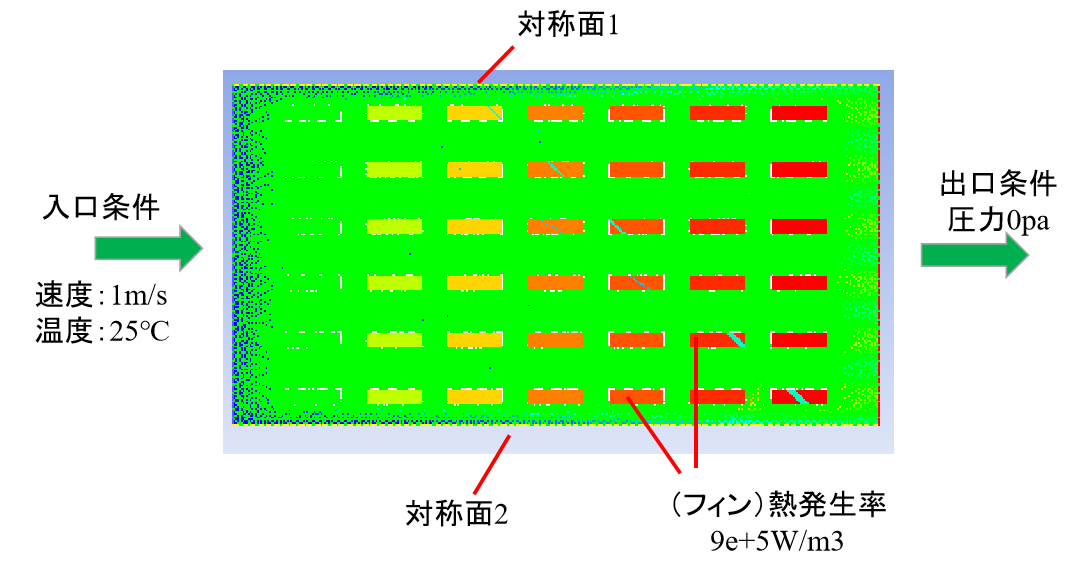
図4:解析条件
メッシュ作成、ソルバーおよびポスト処理ツールとの連携設定は、CAESESのソフトウェアコネクターで行われ、解析結果に基づいてモデル形状を自動的に調整します。ソフトウェアコネクターには、形状ファイル(CAESESで作成したモデルなど)、CFD解析設定ファイル、設計目標ファイル、CFD結果ファイルをそれぞれ配置することで、外部ツールと接続することができます。
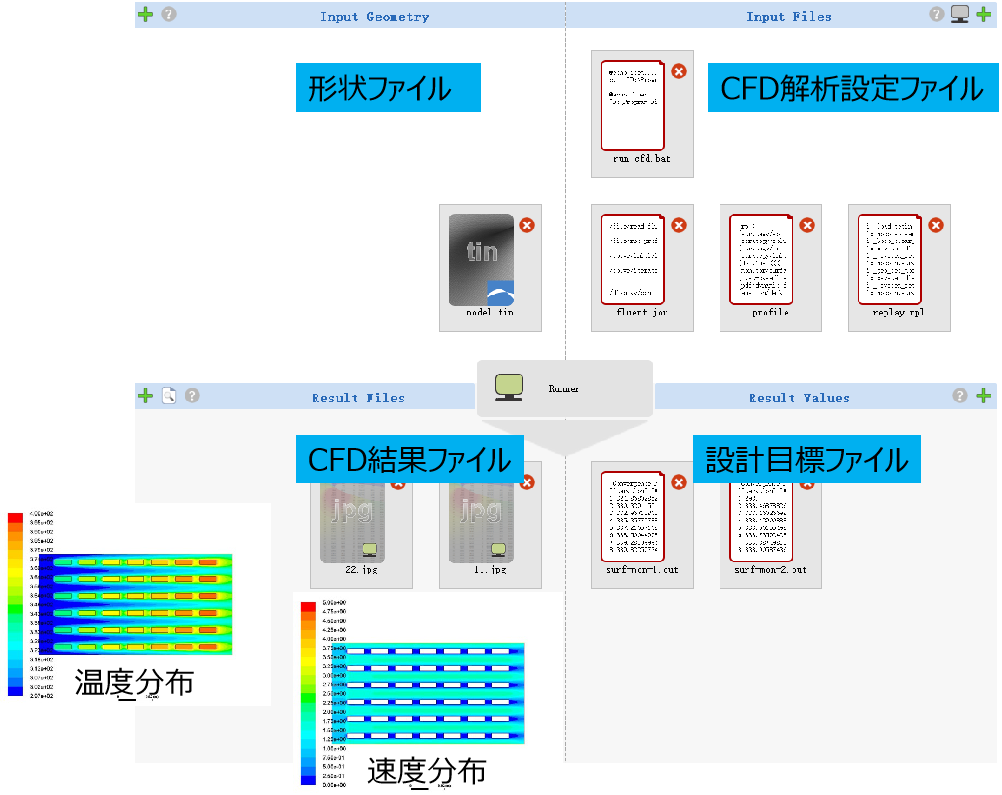
図5:CAESESの外部ツール連携画面
最適化計算では、平均固体温度を目的関数、フィン長さ、幅、配置角を設計変数として、まずは実験計画法(Sobolアルゴリズム、50ケース)を実行し、各設計変数の感度を確認(感度分析)しました。Sobolなどの実験計画法に加えて、CAESESには単目的および多目的最適化アルゴリズム(勾配降下法、遺伝的アルゴリズムNSGA-II、MOSAなど)が搭載されています。
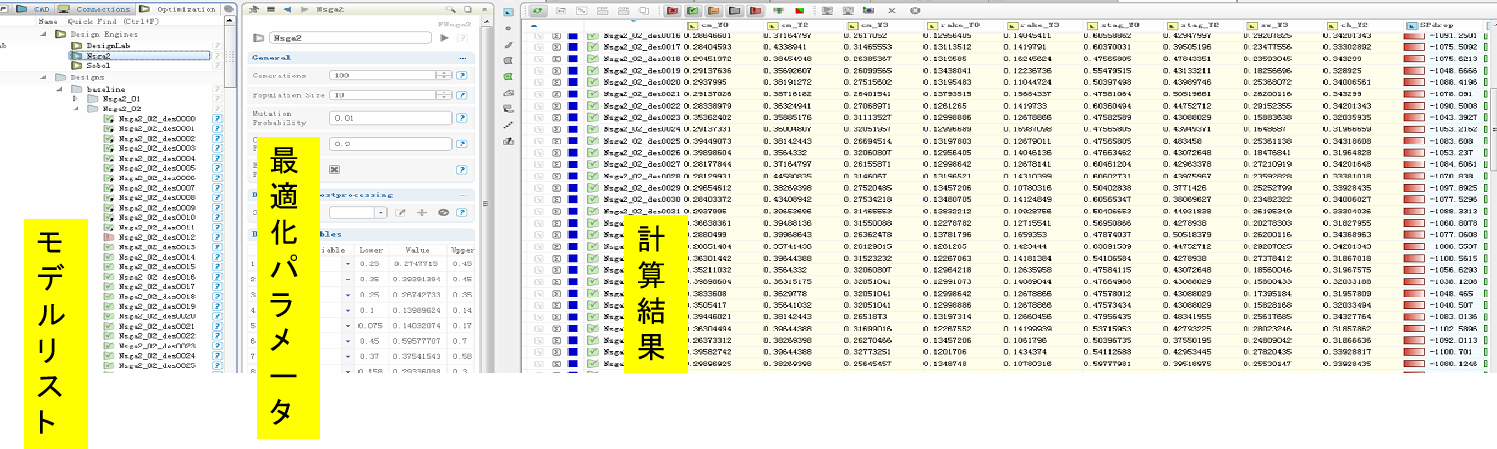
図6:最適化計算時の探索画面
最適化結果
最適化計算により、局所最大温度が2℃低下し、さらにバッテリー全体の平均温度は48℃から38℃へと10℃の低減が確認されました。この温度低減により、バッテリーの温度分布が均一化され、冷却効率の向上が実証されました。さらに、最適化を通じて、フィンのサイズや設置角度が放熱能力に大きく影響を与える要因であることが明確となり、今後の設計最適化において重要な指標となります。
シミュレーション駆動型の最適化を活用することで、設計初期段階から効率的な冷却性能の評価が可能となり、より高性能なヒートシンクの開発やバッテリーシステムの信頼性向上に貢献することが期待できます。
図7~10:実験計画法結果の一部抜粋
図11~12:初期形状と最適形状の温度分布比較